Occupational Health and Safety System
In accordance with the Industrial Safety and Health Act, FANCL Group has established an occupational health and safety system and holds monthly health and safety committee meetings at each of its ten operational sites. The general secretariat compiles information, which is then reported to the FANCL Management Strategy Conference, including the President and Representative Director, by the General Health and Safety Manager.
The committee establishes basic issues and conducts risk assessments related to safety and health so that the company and employees can work together to create a safe, comfortable, and pleasant work environment and ensure health. In addition, the committee conducts workplace patrols to prevent accidents involving employees engaged in all business activities, and if an accident should occur, the committee investigates, follows up, and improves the situation promptly and appropriately.
Occupational physicians and public health nurses also participate in the committee, giving lectures on workplace hygiene (sharing information and alerting employees to seasonal infectious diseases such as influenza) and other topics depending on the external environment. We have created an environment where employees can easily seek advice outside of committee meetings by making information available on the company intranet.
In addition, through our Trading Partner (Supplier) Guidelines, we are further strengthening our existing efforts by requesting suppliers to understand and adhere to the creation of a healthy working environment and health maintenance, as well as confirming the status of compliance with and application of the FANCL Group Sustainable Procurement Policy, including compliance with the Industrial Safety and Health Act. We are also working to further strengthen our existing efforts.
We have been providing education through videos on maintaining and improving health. In the fiscal year ended December 2024, these have been watched by 2,083 employees.
We also provide managerial training on topics such as the duty of care for safety, measures to avoid overwork, and health management through reporting lines. In the fiscal year ended December 2024, this training was taken by 9 new officers.
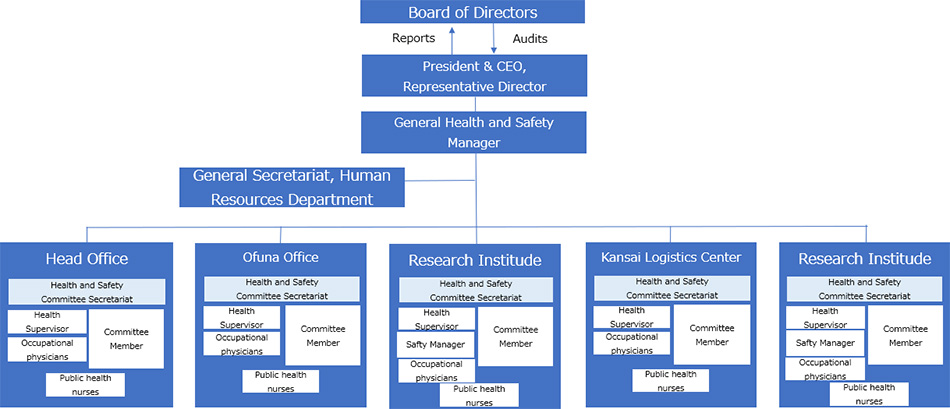
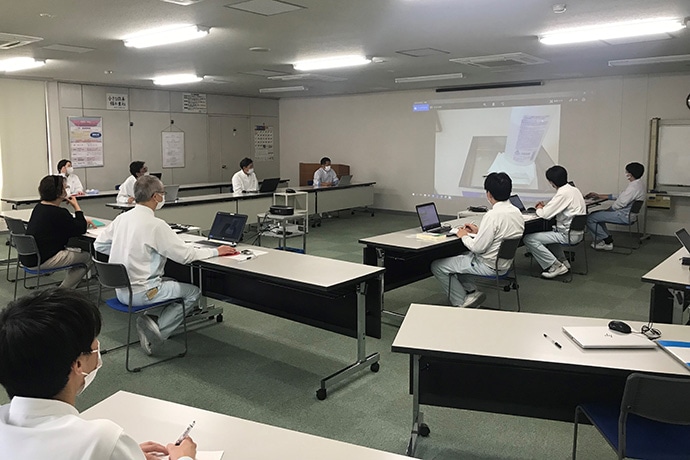
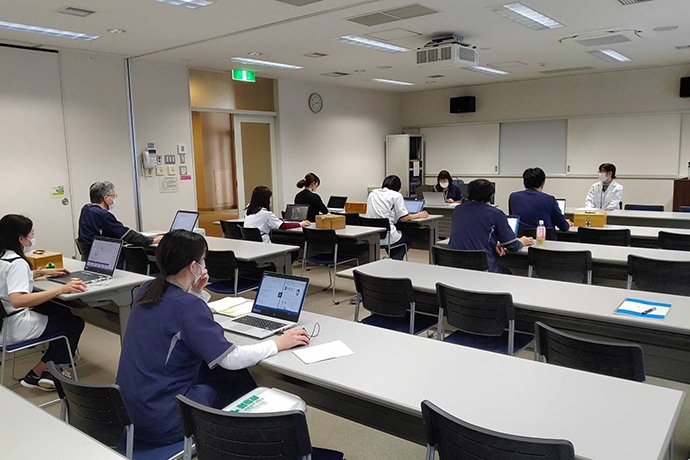
FANCL Group occupational health and safety measures
Improving stairways to prevent falls
The difference in height between steps at the entrance to the kitchen in the company cafeteria posed a risk of falling to kitchen staff. The staircase has been upgraded to have steps that have no height difference (2 steps), which allows safe entry and exit and prevents falls among kitchen staff.
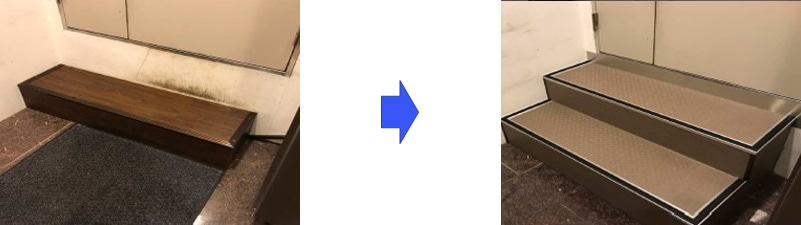
Prevention of health issues caused by localized airflow from air conditioners
Localized airflow from air conditioners at our Head Office was exposing certain seats to cold air, causing health issues for some employees. Because of this, we switched from two-way airflow to four-way airflow.
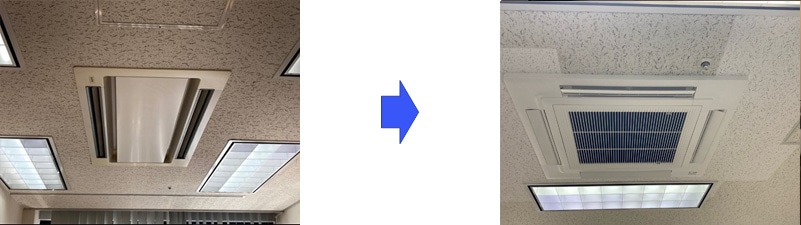
Noise and dust check for new grinder installation
A new grinder for cosmetic containers collected from customers was installed in 2022. Noise levels exceeding 85 decibels were generated during operation, so soundproof panels were installed in the room and we have confirmed a subsequent reduction in ambient noise to below 80 decibels. We have also confirmed that there are no issues with dust generation, which is at less than 0.15 mg per m3.
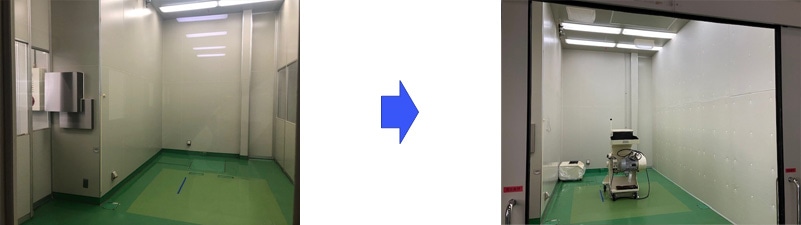
Calisthenic exercises as part of the Ministry of Health, Labour and Welfare's STOP! Injuries from Falls project
At FANCL Biken factories, callisthenic exercises are performed before starting work in order to prevent accidents like falls and tumbles in addition to preventing back pain. Employees carry out calisthenic exercises before starting work in order to prevent accidents like falls and tumbles and to avoid back pain.
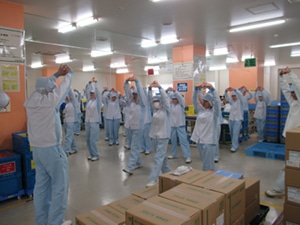
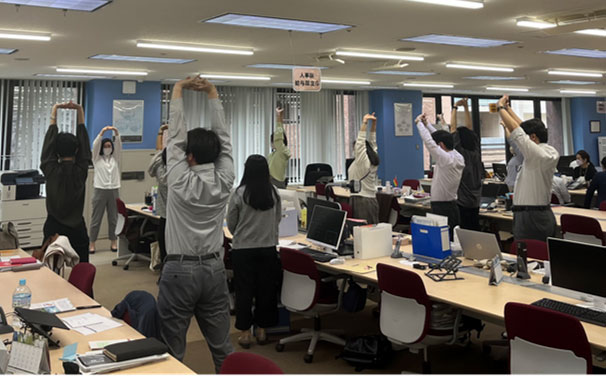
'Near Miss' initiatives at FANCL Biken
In order to further improve quality and realize a safe and comfortable workplace, FANCL Biken keeps daily records of 'near-misses' that may lead to an abnormality or accident. Up until 2021, each plant kept its own records, but in April 2022, we introduced a cloud service to share information digitally at all plants. The latest data is always visualized in graphs and tables, and all employees can check the data, leading to speedy workplace improvements and accident prevention.
Pointing and naming as part of hazard prediction activities
As part of hazard prediction activities at FANCL Biken factories, workers point out objects and instruments used for work, confirming their names and conditions aloud.
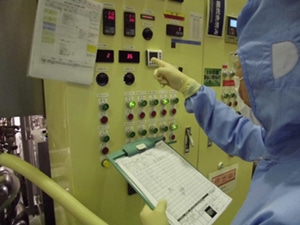
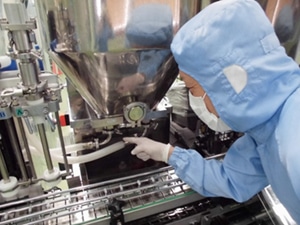
Item | FY 2023 Actual |
FY 2024 Target |
FY 2025 Target |
FY 2030 Target |
|
---|---|---|---|---|---|
Countermeasures Against Infectious Diseases | Number of Outbreaks |
0 Cases |
1 Cases |
0 Cases |
0 Cases |
Overtime Work | Average Monthly Overtime Hours |
4.9hours |
4.7hours |
3.5hours |
3.3hours |
Paid Leave Taken | Average Rate of Paid Leave Taken |
83.0% |
80.6% |
84.0% |
90.0% |
Extended-Length Work Interviews | Number of Extended-Length Work Interviews |
2Number |
1Number |
0Number |
0Number |
Occupational accidents | Occurrence rate (lost days) |
0.9% |
0% |
- |
1.0% or below |
Occurrence rate (deaths) |
0% |
0% |
- |
Maintained 0% |
The Health and Safety Committee reports on the results of each item for each business site. In particular, we focus on sharing case studies covering occupational accidents to ensure prevention of recurrence and continuous improvement.